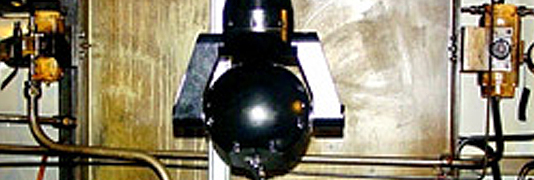
At the same time, the hazardous environment created while a plant is operation can make it difficult or impossible for engineers to check equipment and track down any faults - and remote monitoring devices can often give insufficient visual clarity or limited visibility range to diagnose potential problems accurately.
This was the challenge facing global power generation company InterGen at its power plant in Spalding, Lincolnshire. Spalding Energy , which began commercial operation in 2004, is one of the most modern and efficient in the UK.With an output of 860 MW, it uses a combination of gas turbines, heat recovery steam generators and steam turbines to supply energy into the UK National Grid.
"Our two gas turbines operate practically around the clock," says Ged Button, LTE engineer at the plant. "When they're running, it's against site procedures for anyone to enter certain areas inside the installation because of the potential risks. At the same time, we needed to be able to monitor equipment constantly in these areas."
The solution was a Forward Vision MIC1-440 ATEX certified camera. This range of cameras meet the stringent ATEX Directive 94/9/EC Exd IIC T6 for safe use in explosive atmospheres like those found in oil, gas, chemical processing sites and petrochemical refineries. They are precision engineered to deliver 360º continuous rotation pan with 320º tilt and zoom in on precise spots, allowing a remote operator a complete, panoramic view of the area they survey.
A camera was installed by MV Tech in each of the two gas turbine fuel gas skids at Spalding and within a few days it amply justified its presence.
"We discovered a slight oil leak," says Ged Button. "A few days after the camera was installed, we found a small pool of oil on the floor near some piping. Our engineers knew that the leak was almost certainly caused by a change in oil pressure, which manifested itself when the machinery was running. When it was offline, it was impossible to see where the leak was happening. We needed to be able to observe the section of installation near to the pool of oil while the plant was running. It was an ideal job for the camera."
The camera was directed at the suspect area of piping once the plant was fired up again, and the operators were able to zoom in closely to examine all the joints. The camera's excellent images enabled them to identify the place where the oil was leaking almost immediately. The plant was shut down once more and the repair swiftly and efficiently completed. Afterwards, the camera was used to ensure that the repair was effective.
"Unplanned shutdowns can have a major impact on Spalding's commercial business," adds Ged Button. "Although the leak was small, problems like this have to be rectified immediately for obvious safety reasons. Without the ability to diagnose the problem safely and remotely, it could well have cost InterGen many thousands of pounds to attempt to locate the leak while the plant was offline."
Contact us
Telephone us on +44 (0)7909 684 436 or Email us at info@mvtech.net or Use the form below and we'll get back to you as soon as we can.