Forward Vision’s MIC1-440 ATEX certified Metal Mickey helps energy plant safety

Safety is a vital concern for the energy industry. When potentially flammable materials such as oils and natural gas are used in generating power, the need to maintain all plant, equipment and machinery to the highest level of excellence is an absolute priority.
At the same time, the hazardous environment created while a plant is operation can make it difficult or impossible for engineers to check equipment and track down any faults - and remote monitoring devices can often give insufficient visual clarity or limited visibility range to diagnose potential problems accurately.
This was the challenge facing global power generation company InterGen at its power plant in Spalding, Lincolnshire.
GE Frame 9 Gas Turbine - Exhaust Thermocouple Upgrade
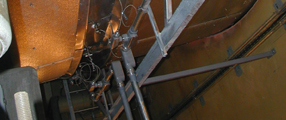
Exhaust thermocouples provide the raw data used to estimate the firing temperature at the exit of the first stage nozzles. The average of the exhaust temperature measurements, along with the pressure ratio, allow the firing temperature to be estimated. This is critical as the service life of all the combustion liners, transition pieces, nozzles and buckets are all directly related to the firing temperature.
In recent years, several of our clients have upgraded their exhaust thermocouple systems to a new type AMETEK hermetically sealed thermocouple which offers longer product life and improved accuracy. The new system also has stainless steel braid protection on the cables and captivated hardware for ease of maintenance.
Engineer out a problem with the Gas Turbine Purge and Vent valve systems.
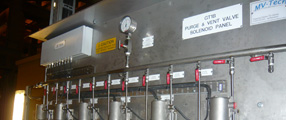
Electrically operated solenoid valves are used to control the air supply to pneumatically driven valves located in the Fuel Gas module. The fuel gas to this module is preheated prior to entry and thus the internal temperature of the module is high, causing the solenoids to fail prematurely.
A solenoid replacement caused the Technician to navigate through various controls equipment as the previous arrangement was extremely difficult to work on. The Fuel Gas module is also classified as a Zone 2 area ( ATEX regulations) and therefore requires considerations and suitable measures to be put in place to allow work to be carried out in this area.